 |
 |
 |
 |
 |
 |
 |
 |
 |
 |
 |
 |
 |
 |
 |
 |
 |
 |
 |
 |
|
|
|
|
|
|
|
|
|
|
|
|
|
|
|
|
|
|
|
|
|
|
|
|
|
|
Home Machine Tool
Archive Lathes for Sale
Millers & Grinders for
Sale E-MAIL tmailto:Tony@lathes.co.uk
Bridgeport
Milling Machines
Milling,
Drilling & Boring Heads Models M, J, 2J and 2J2
Page 1 of 2
Click HERE for
Page 2 Milling &
Drilling Heads Cherrying &
Slotting Heads Head
Attachments Head
Adaptors
Bridgeport Home
Page Accessories
Measuring
Equipment Quick-set
Tooling Horizontal
Miller
Round-ram
Model Table Power
Feeds Collets &
Adaptors At
Work Right-angle
Drives Serial
Numbers Hydraulic
Copying, NC and other Special Machines Handbooks and Parts Lists
are available for most
Bridgeport machines
A range of
different heads and head accessories has been available for the
Bridgeport since its introduction, allowing the customer to choose
between heavy-duty, fixed-quill models and very high-speed
"sensitive" units with either (or both) power down and up feeds and
hand operation though worm-and-wheel fine-feed or quick-action,
sensitive drilling mechanisms. Heads were at first available with a
choice of either a No. 2 Morse taper, or Brown & Sharpe No. 7 or
B-3 tapers but later the "designed-for-Bridgeport" R8 fitting became
the standard. Whilst some heads will fit only on the front of the
ram, others can be mounted on the back as well; details of the
adaptors that allow rear mounting can be found here. In
the past a variety of heads were been available, including: Model
M*, the original head - see the bottom of this page. Model R for
heavy-duty use, but with a fixed quill. Model C*
for light-duty, high-speed use, with a sliding quill. Model T for
Cherrying. *can be mounted at rear of the ram. For many years
the standard head was the V-belt drive "Type J" fitted, for
slow-speed work, with a lathe-like backgear assembly. This was
joined by what was, at first, listed as the "Type J Varidrive" but
later called the "2J": fitted with expanding and contracting pulleys
this provided, in conjunction with its standard fit backgear, two
infinitely-variable speed ranges that ran from 50 to 450 rpm and, in
direct drive, 450 to 3750 rpm - though small changes in the
mechanical specification (and the type of electricity supply)
dictated that these ranges did vary somewhat from country to
country. By the 1990s the "regular" head had become the infinitely
variable speed 2 h.p. Model 2J2, or, at a saving in cost, its less
powerful predecessor the Model J with 12-speed V-belt drive. The J2J
and 2J both had hand-operated and power feeds - and both
quick-action drilling and fine-feed quills. To increase the
versatility of these heads a special right-angle extension drive,
the "Quillmaster", used to be available and even this could be
further modified by the addition of a right-angle tip drive, the
"QRA" or "Quillmaster Right-angle Attachment". Details of the
Quillmaster and its capabilities can be found here.
Also available for many years was the Model T
slotting and forming head. For new Bridgeport owners it is worth
noting that, whilst the speed setting dial for the variable-speed
head can only be turned whilst the motor is running, to engage
backgear (and the slow speed range) the head should be stopped and
the spindle "jigged" backwards and forwards until the gears engage.
Importantly, in backgear, the spindle runs in the reverse direction
to normal and hence the reversing switch has to be used to get the
cutter rotating
correctly.
|
| |
|
|
|
|
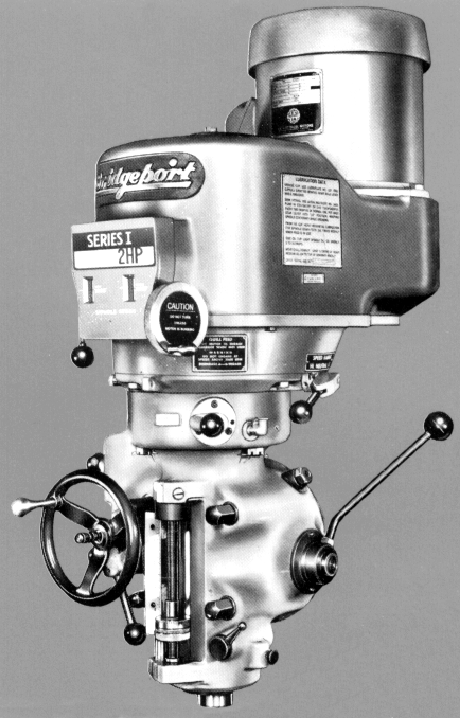 |
|
|
|
|
|
|
|
For
most late-model machines the Model 2J2 was the "Standard" head
offered for the Series 1. It had a 2 hp. (1.5 kW) motor driving an
expanding and contracting pulley system, incorporating a lathe-like
"backgear", to give infinitely variable speeds from 50 to 3750
rpm. Like all Bridgeport heads the quill was hard-chrome plated,
ground and then lapped to fit the honed bore in the main casing. The
handles of both the quick-action drilling ("sensitive") and
wheel operated fine-feed were detachable and three rates of power
down (and up) feed provided. The spindle was fitted with a brake
- to slow it rapidly from high speeds - that could also be
positively locked to aid tool changes; a clutch, designed to slip in
overload conditions, protected the spindle from
damage.
|
|
|
| |
|
|
|
|
|
|
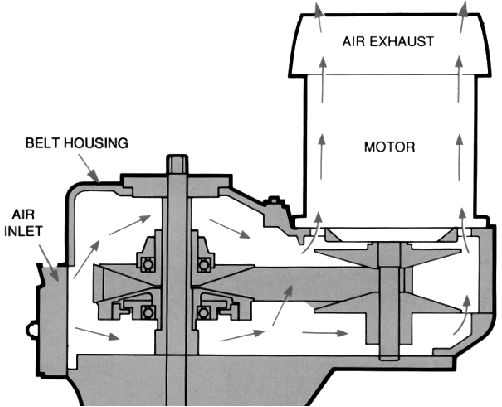 |
|
|
|
|
|
|
|
|
2J2
Head showing the disposition of the variable-speed drive and
air-flow route through the head and motor.
|
|
|
| |
|
|
|
|
|
|
|
|
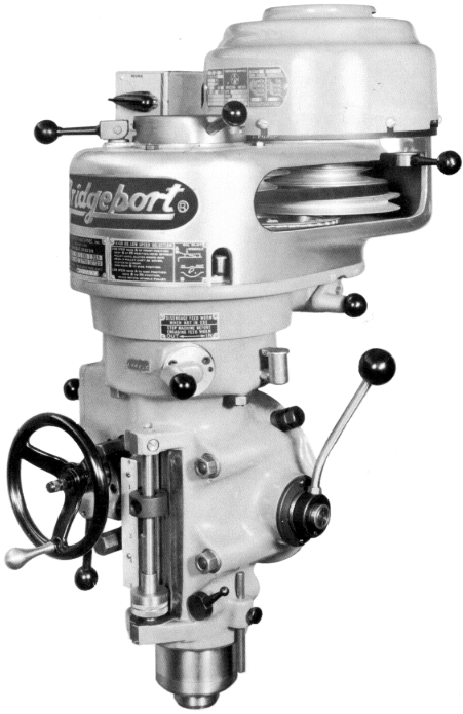 |
|
|
|
|
|
|
|
|
|
|
|
|
|
|
|
|
|
Above: Model J Head This unit, after the original M head
and before the introduction of the variable-speed 2-hp head, was the
standard Bridgeport fitting but was then offered as a cheaper
alternative to the 2J2. The counterbalanced R8 quill - hard-chrome
plated and ground, then lapped to fit the honed spindle bore - had
5-inches travel and was fitted with both hand and power feeds. The
hand feed could be applied through either a quick-action lever when
drilling - or by a handwheel for fine feeds. The power feed, at the
rate of 0.0015, 0.003 and 0.006 inches per spindle revolution,
worked in both directions and could be set to trip out
automatically; a 0.001" graduated micrometer stop was fitted as
standard. A wide range of spindle adaptors
was available to mount a variety of tooling. Whilst the
specifications of more recent versions of the head varied, in the
past a choice of two 1 h.p. motors, each wired for reverse, was
offered (and others, possibly, depending upon the year of
production); a 1800 rpm unit that gave (in direct drive and
"backgear") spindle speeds of 80, 135, 220, 330, 660, 1100,1800 and
2720 rpm - and a 3600 rpm version that had the effect of doubling
each of the aforementioned speeds. When vertical, the head could
be run continuously - but needed modification to the
lubrication system if used in the same way
horizontally.
|
| |
|
|
|
|
|
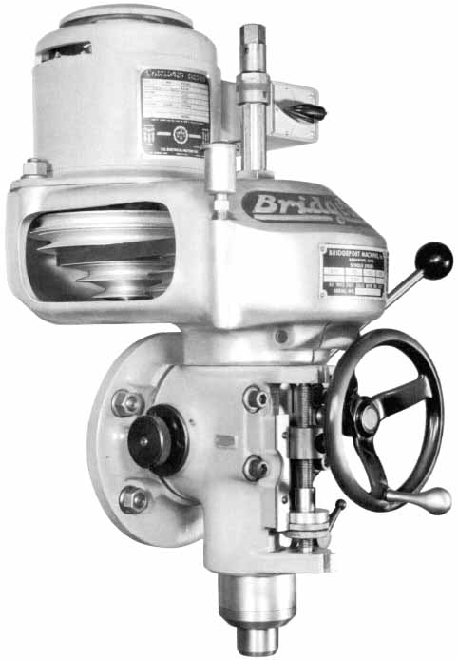 |
|
|
|
|
|
|
|
|
Model M Head This was the head fitted to the first
Bridgeport milling machines and had 3.5-inches of quill travel
through both fine and quick-action feeds by hand operation
only. The spindle could be ordered with a No. 2 Morse, B & S
No. 7 or a B-3 taper - and the maximum collet capacity was 0.5
inches. Special tapers were available to order and it is highly
likely that a factory already equipped with tooling to a different
specification might have ordered its machines so as to be able to
mount cutters already in stock. The 0.5 h.p. motor was available
as either a 1200 rpm unit - which gave spindle speeds of 275, 425,
700, 1050, 2100 and 4250 rpm - or as a 3600 rpm model with rather
higher spindle speeds of 950, 1350, 2200, 3250, 6500 and 12000
rpm. The unit could be mounted either on the front or back
of the ram and, if on the latter, fitted to a swivel adaptor that
allowed it to be angled in both planes. Details of the various
head mounting adaptors can be found here.
|
|
|
| |
|
|
|
|
|
|
|
|
|
|